On the way to a decarbonised economy, green hydrogen is seen as a source of energy and hope at the same time. However, the need for hydrogen electrolysers and hydrogen-ready plants currently significantly exceeds engineering and production capacities. Consistent data centricity for more efficient, modular engineering processes can significantly reduce the gap between supply and demand, says Reinhard Knapp, Head of Global Strategies at software provider Aucotec.
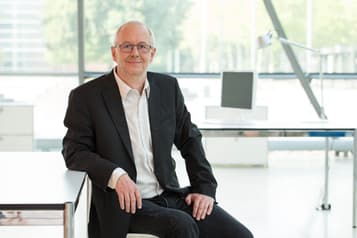
Reinhard Knapp © Aucotec
The answer to many questions surrounding decarbonisation is hydrogen: whether as a fuel in passenger and freight transport, as an energy carrier in industrial plants or for the low-loss storage and safe transport of renewable energy.
Where are the sticking points?
The theory is optimistic, but in practice the sticking points are the nationwide hydrogen network, the lack of mobile fuel cells and plants capable of using hydrogen, but above all there is a lack of sufficient green hydrogen, because, “There is still far too little electrolysis capacity on the market for the necessary quantities,” says Knapp. Which is why the company has set itself the mission of enabling electrolysis plant manufacturers to increase their capacities significantly faster.
More efficient engineering for more megawatts
In addition to improvements in electrolysis technology, optimised engineering processes for the associated plants can also make a decisive contribution to this. And it’s urgent.
“We are being contacted by interested parties who want to have their production capacity multiplied as soon as possible, in order to be able to supply more electrolysers annually for significantly more megawatts of power,” reports Knapp. His and Aucotec’s answer to this is the data-centred cooperation platform, Engineering Base (EB). “Its principle of the object-oriented data model is the foundation for considerably more efficient, more agile plant development and an exceptionally clear form of modular engineering,” said the Head of Global Strategies.
Many players on the market are still struggling in terms of plant development with insufficient tools and data models, some of which require manual intermediate steps. On the one hand, these are new plant manufacturers who may be well versed in hydrogen technology, but who are entering uncharted territory when it comes to engineering.
On the other hand, many experienced machine and plant manufacturers are still engineering out of habit with their document-oriented tools, which were often designed decades ago, and are shying away from the effort required for a transformation. Knapp is convinced that these companies could participate significantly more in the hydrogen market ramp-up with more up-to-date engineering. Even operators who must convert their existing plants to use hydrogen would benefit.
Safe, simultaneous, agile across disciplines
Modern engineering, as Aucotec understands it, is based on a central data model. All the disciplines involved work on this together and simultaneously – from the first plant concept to commissioning. Every change and addition, no matter where it was made, is immediately visible and traceable for all parties involved in all other representations of the planning object. Therefore, EB’s consistent model of devices, functions and its complete network of relationships, right up to automation, provides an optimal basis for efficient, agile teamwork.
“Because error-prone data transmissions or duplicate entries as well as complex coordination processes are eliminated,” Knapp emphasised. And not only users can always rely on the data quality. For example, EB offers project managers the opportunity to retrieve the current status of their projects at any time, even without deep system knowledge.
Scaling by multiplying
The overarching data centricity also greatly benefits modular engineering – an important point for electrolysis plant planners. They tend to organise their projects in line with the product world and want to work with highly standardised modules that ‘click together’. After all, they cannot, as in the case of chemical plants, simply design a reactor larger in order to produce more. Instead, they scale plants and output by multiplying the modules.
Weeks instead of months
EB has learned a lot about modularity in the automotive industry, as well as in energy distribution, where the platform has been at home for decades. There is also a suitable variant for process technology, which is used by many large EPCs and operators. One of them is Topsoe, also a sought-after electrolysis expert. The Danes put it down to EB that some work takes only six weeks instead of six months, mainly thanks to the overarching “data home”.
Simply click together and create a network?
When it comes to modular work, two aspects are elementary: on the one hand, the creation of the individual modules and their availability. On the other hand, assembling and networking them to form a plant unit.
In the past, when reusing module documentation, a lot of papers, at best PDFs, had to be collected, copied and edited from various discipline-specific tools. Then the marking of components alone was tedious and error-prone, since it had to be changed by hand. Instead of project-related documents from various tools, EB’s library contains the complete digital data models of tested modules with all electrical, process and automation information. Variants with the feasible options are also stored and they can be conveniently configured and adopted via Typical Manager.
“Once the modules have been designed in EB, 90% of the work is done and assembling them into the desired plant becomes almost child’s play,” said Knapp. Just select the modules, put together the project – the names of the devices adapt themselves independently – and make the higher-level connection. The modules and their connections fit seamlessly into the overall concept. Everything in just one system, even the control system configuration. The documentation for this largely comes about by itself.
Hydrogen-ready faster with the latest digital twin
The customers of hydrogen as an energy carrier for their plants get less help from modular design. However, operators are facing extensive conversions. For this, it is essential to have a reliable as-built documentation system, in the best case here also a directly editable, cross-discipline plant model, i.e. a digital twin. EB makes this available, either developed directly in the system or by migrating old data, whereby an interface digitally processes and upgrades the existing information.
In addition, the system makes it easier to keep the twin up-to-date with its maintenance app. After all, its value is determined by how reliable and up to date the data is. The usual plans, which are often changed by red entries in their discipline-specific silos, are anything but helpful. Then it would be better to stay continuously ‘on the ball’ using a data model. “In this way, reliable information is immediately available, even in an emergency,” Knapp stressed.
More time for the essentials
So, whether manufacturers of hydrogen plants or users of the energy carrier, both sides have more time for the essentials with data-centred engineering: on the one hand, to build more and better electrolysis plants in a shorter time, on the other hand, to build more plants faster and ready for hydrogen to enable them to be operated with green hydrogen. Our environment could use it.
H2 View’s Premium Subscription
If you’re looking to upgrade your H2 View experience, our Premium Subscriber package provides you with all the unparalleled insight of an essential package but with the added opportunity to help Make Hydrogen Happen!
With our Premium Package, you will gain access and discounted rates to H2 View’s in-person and digital hydrogen summits:
- Unlimited access to h2-view.com, including subscriber-only content
- Monthly digital and/or print magazine
- Subscriber-access to H2 View Snap Summits (digital events)
- 20% off all H2 View in-person events individual tickets
Click herefor more information on the package or you can contact H2 View’s Subscriptions Manager, Jordan Pooley: [email protected].