At first, I almost felt bad jumping onto a call with Tony Cochrane, Chief Commercial Officer (CCO) at Ceres. It was 4am in British Columbia when he joined our call. But, loaded up with coffee and looking remarkably fresh, he was quick to dismiss my apologies.
He had been up for several hours, following the announcement that the company had signed a long-term manufacturing collaboration and license agreement for its solid oxide electrolysis cell and fuel cell (SOEC and SOFC) stack production with Delta Electronics.
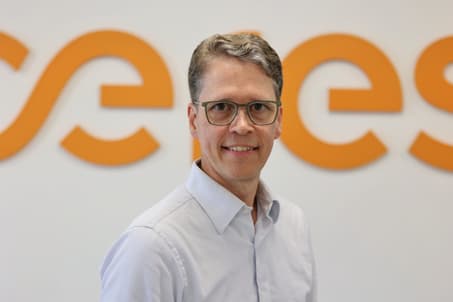
© Ceres Power | Tony Cochrane, Chief Commercial Officer
The deal announced on January 18 marked another step fowards in the company’s plans to build up its ecosystem of global licence partners laying down manufacturing stack production – following similar fuel cell licensing agreements with Bosch and Doosan.
Under the agreement, technology introduction and factory construction will start this year and initial production by Delta is expected to start at the end of 2026. Ceres will receive an initial £43m ($54.8m) of revenue, as well as royalty payments from Delta on future commercial production and sales to end customers.
Given its previous licensing partnerships, Cochrane told H2 View, Ceres knew just what it takes to establish a factory to mass-manufacture its technology.
“There are a lot of good reasons why we might target a partnership with Delta,” he said. “They’ve got a strong pedigree in manufacturing with precision and scale, and importantly driving costs down.”
our focus is to deliver them best in class technology and really robust manufacturing capabilities and blueprints that they can replicate with their own equipment
The Taiwan-based company boasts over 200 sales and distribution sites globally. With a market capitalisation of around $23bn, Delta has previously specialised in the mass manufacture of power electronics and data centres for customers including Microsoft.
Cochrane said, “This is one of the benefits of our licensing model. We don’t need to take investor capital and put it into buildings and factory equipment. We rely on our partners to do that work and our focus is to deliver them best in class technology and really robust manufacturing capabilities and blueprints that they can replicate with their own equipment, develop their own supply chain and then manufacture and sell the product.”
Previous Doosan and Bosch agreements
In 2019, Ceres signed a collaboration agreement with South Korea’s Doosan for fuel cell technology. The partners agreed to jointly develop a 5-20kW low-carbon power system for use in the commercial stationary power market. In 2020 Doosan acquired a licence to manufacture Ceres’ SOFC stacks.
Building off a joint development agreement (JDA) signed with Bosch in 2018, the German multinational took a 4% equity stake in Ceres building it to 18% in early 2020 when the partners announced that Ceres would transfer its SOFC technology and licensing to Bosch for the low-volume production of the fuel cells for stationary power. Bosch’s 200MW SOFC manufacturing facility, which has received €160m ($174.3m) of European funding, is due to start production at the end of 2024.
As the conversation went on, it became all the more apparent that Ceres’ model allows a significant focus on technology.
CAPEX and OPEX savings
SOEC is a high-temperature electrolysis method for hydrogen production. Using a solid ceramic material as the electrolyte, electricity splits water under temperatures of up to 800oC. The temperature can significantly reduce the electrical energy required, making the process more efficient than low-temperature electrolysis.
“People should remember, SOEC produces hydrogen with about 20-25% less green electron input costs,” he said. “The cost of green electrons is the lion’s share of the green hydrogen cost. So, any device that can save a producer 20% of that component of their costs is going to highly competitive to the incumbent technologies of alkaline and PEM.”
But, at the heart of Ceres’ technology are certain features that look to maximise efficiency and material savings to deliver a product that could challenge many players on the market.
“Ceres operates at the lowest temperature,” Cochrane remarked. “Our technology operates in the 550-650oC range, and that has some really interesting practical reasons to succeed, meaning we get maximum efficiency out of solid oxide.”
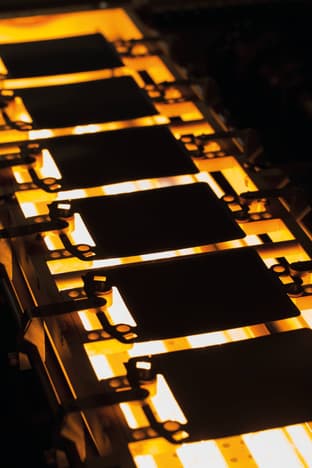
© Ceres Power
“You have to harvest heat from the industrial process that you’re coupling it with. For example, in an ammonia plant, the Haber Bosch synthesis process is generating heat. You can take that heat and use it to improve the efficiency of the hydrogen production. Harvesting heat at Ceres’ temperature domain is much easier than trying to find 750-800oC, which all the other major SOEC companies need.”
Not only does the lower high-temperature process improve efficiency and reduce heat finding burdens, but Cochrane told H2 View it reduces the cost of components in the electrolyser, while also improving cell manufacturing.
He said, “If all the components have to withstand 800oC, you’re talking about all of them being very expensive because they are more exotic materials. Whereas Ceres uses conventional steel piping. Even the cells themselves are essentially stainless steel. So, we can offer the same efficiency as all the other solid oxide solutions, but the cost of the asset is much lower.”
“Because our cells are made as a metal substrate with a thin layer of ceramic on it, it’s a very robust manufacturing process which is scaled more easily. It’s easier to meet high quality standards.”
“I think that’s what attracted companies like Bosch, Doosan and Delta to Ceres technology,” Cochrane said.
What this feeds into, in Cochrane’s view, is a product that could combat some of the challenges facing electrolyser project developers.
H2 View has increasingly heard that higher CAPEX costs, EPC costs and renewable power costs have made the economic environment more difficult for renewable hydrogen.
Despite a 35% growth in the global hydrogen project pipeline, the Hydrogen Council’s December 2023 Hydrogen Insights report said just 7% had passed final investment decision (FID).
We can’t control the risks, but what we can control is the reward through higher conversion efficiency and lower capital investment
He said electrolyser companies sit between two economic factors: the supply of cheap green electrons and hydrogen offtake at a price that “rewards the investment.”
Following the EU’s RFNBO delegated acts and the US’ proposed 45V tax credit rules, Cochrane described the incentive environment as somewhat unstable. “When your input costs and sales prices are bouncing around, people get nervous and wait,” he said.
“It’s not a single company problem…All of these projects have very sophisticated FIDs that contemplate risks and make decisions on whether they’re bankable or not. We can’t control the risks, but what we can control is the reward through higher conversion efficiency and lower capital investment.”
And thanks to those efficiency gains and lower capital costs, Cochrane is confident there are projects on the side lines that haven’t met bankability requirements that could come into play with the employment of Ceres technology.
More work to do
Aside from the big licensing deals, system testing continues to be a major focus of the company.
Last November (2023), Ceres announced a 1MW electrolyser demonstrator was in the final stages of commissioning. Having produced hydrogen at AVL’s test site, the system was en-route to Shell in Bangalore, India, for installation.
“Now it’s just a matter of installing, doing the final commissioning on site, turning it on and starting to generate very valuable data,” Cochrane said. Valuable because he said the data will be needed to convince conservative industries that the technology is “ready for deployment and scale.”
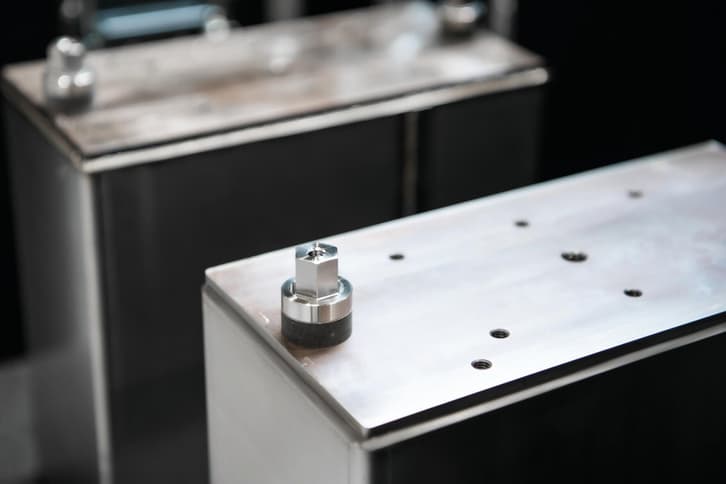
© Ceres Power
In addition to the system destined for Shell, Ceres is also pursuing an electrolyser programme with Linde Engineering and Bosch in Germany. And he believes, that between the two programmes, it will help inform decisions for their new licensing partners.
He said, “We’ve got a signed deal with Delta, but that’s just the start of the journey. It’s exciting, but we have got a lot of work ahead of us to help them to build the factory that they’re minded to build by 2026. The reason we can do it more quickly than we have in the past is because we’ve harvested the learning curve from our first two licenses.”
“We’re a very systems engineering focused company,” he said. “Even though we focus primarily on the core technology, we know that technology needs to be compatible with the end-use application.”
“We need to cascade application requirements back through to make ourselves more robust. Whether its contaminants, operating modes or steam qualities, there’s a number of things that we learn from our partners that help us make better cells, stacks and designs.”
Wider partners are also a main focus of the company moving forward as it looks to capture the SOEC market.
Cochrane told H2 View, “Ceres’ belief is that if we can get our partners to market before other solid oxide competitors, with a credible, reliable product that has a strong supply chain behind it, the opportunities will go to them and not some of the competitive SOEC.
“It is a bit of a race. But I think our licensing model allows us to run with multiple partners. If you’re a betting person, it’s a multiple bet versus single bet strategy. And we’re making the bet with people who already know how to manufacture and scale, and who already have supply chain relationships.
“We’re reasonably confident that if we get going, we can win that race.”